Plant & Process
Digital Twins for Oil and Gas
In the oil and gas industry, digital twin technologies help companies improve operational efficiency, enhance safety, reduce downtime, and lower costs.
Predictive Maintenance of Offshore Platforms
Continuously monitor critical equipment using sensor data to detect anomalies and predict when components will fail. Engineers can schedule maintenance before breakdowns occur.
Optimizing Oil Field Production
Simulate reservoir behaviour, well performance, and fluid dynamics, allowing operators to optimize production rates, adjust well placements, and predict the best drilling strategies. Benefits include: increased production efficiency, better resource management, and reduced environmental impact.
Refinery Process
Optimization
A refinery that integrates real-time process data with predictive simulations to optimize refining operations, such as adjusting temperatures, pressures, and flow rates to improve efficiency. Benefits include: higher output, lower energy consumption, and reduced emissions by continuously optimizing refining processes.
Pipeline Integrity and Leak Detection
Digital twins of pipelines can be used to monitor pressure, flow, and temperature in real-time. By detecting anomalies in pipeline conditions, the digital twin can predict and locate potential leaks or failures before they happen.
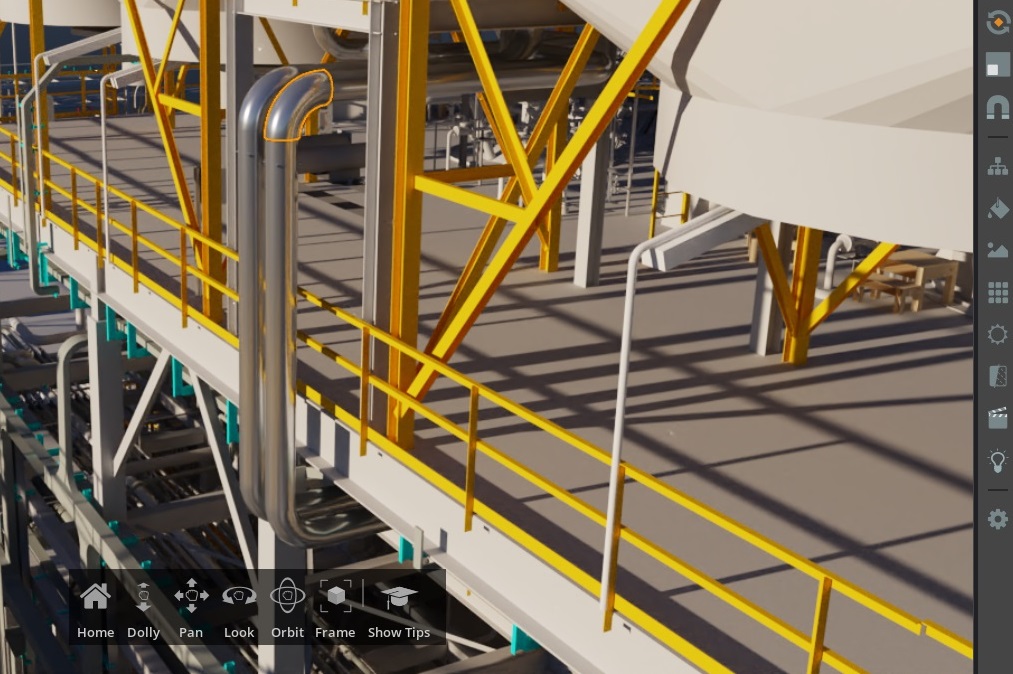
Leverage digital twins to manage operations
Manage operations across the entire value chain, from exploration and production to transportation, refining, and distribution.
Drilling Optimization: a drilling rig digital twin simulates in real-time equipment behavior and wellbore conditions, allowing operators to adjust drilling parameters for optimal performance.
Field Management: Digital twins of oil fields integrate data from multiple wells to simulate fluid dynamics, reservoir behavior, and production rates. Engineers can use these insights to optimize well output, manage resources better, and extend field lifespans.
Failure Prevention: By simulating stress on equipment and identifying potential weaknesses, digital twins enable companies to proactively address maintenance needs and avoid costly equipment breakdowns.
Performance Optimization: By simulating different operational scenarios, digital twins help optimize asset performance, from production schedules to transportation logistics. This is particularly useful in remote or hazardous environments, where on-site management may be costly or dangerous.
Digital Twins in the Chemical Industry
By integrating real-time data, predictive analytics, and simulations, digital twins help companies streamline complex chemical processes, reduce downtime, lower costs, and accelerate innovation. With growing pressure to meet environmental standards, increase efficiency, and maintain high safety levels, digital twins enable companies to manage risks, optimize resource use, and drive sustainable production.
Process Optimization and Efficiency
Simulate an entire production process, enable engineers to adjust parameters like temperature, pressure, and reaction times in real-time. Use simulations to help identify optimal conditions for maximizing yield and minimizing energy use.
Predictive Maintenance of Equipment
Monitor the health of critical assets such as reactors, pumps, and heat exchangers. By collecting real-time data and using predictive analytics, a twin can help you forecast equipment failures, allowing for scheduled maintenance before issues occur.
Safety and Risk
Management
Simulate various risk scenarios, such as equipment malfunctions, chemical leaks, or safety protocol failures and use these simulations to help identify potential risks and test emergency responses, ensuring preparedness for real-world situations.
Sustainability and Emissions Reduction
Model the environmental impact of chemical processes and allow companies to test greener alternatives, such as lower-emission production methods or renewable energy integration. A twin can also be used to track emissions in real-time and provides data to optimize resource use and minimize waste.
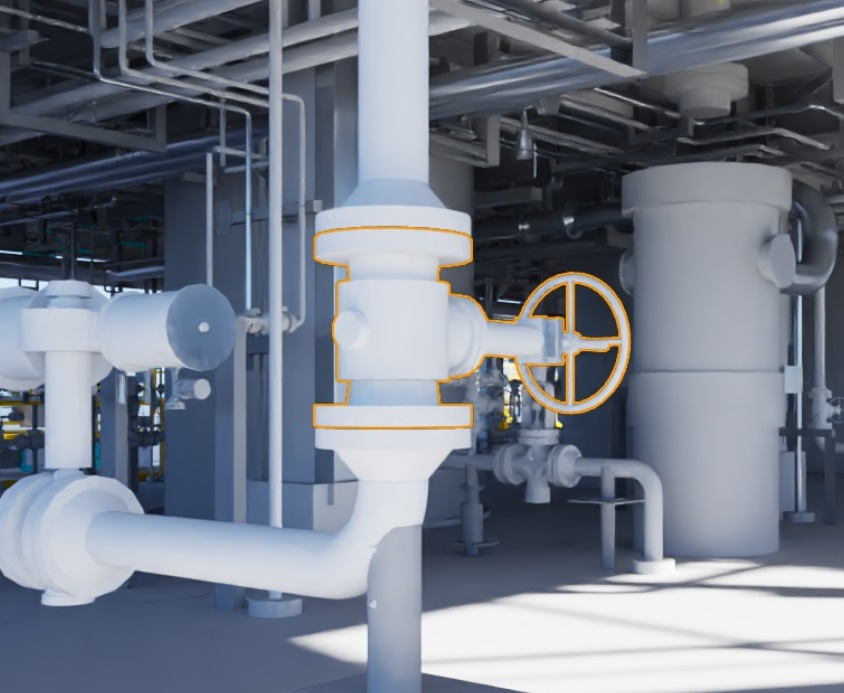
Improve productivity in chemical manufacturing
Optimize productivity by leveraging real-time data, predictive analytics, and simulations to improve process efficiency, reduce waste, and enhance overall performance
Continuous Process Improvement: With real-time feedback from sensors and data analytics, a digital twin can monitor performance and help operators fine-tune production processes, leading to more efficient operations and higher productivity.
Predictive Maintenance Scheduling: Using predictive analytics, a digital twin can help forecast when equipment is likely to fail or need maintenance, allowing companies to schedule repairs before breakdowns occur. This avoids unplanned downtime and ensures equipment operates at peak efficiency.
Inventory and Resource Management: A digital twin of the supply chain can integrate data from raw material suppliers, transportation systems, and storage facilities. This helps companies manage inventory levels, ensure raw materials are delivered on time, and minimize delays in production.
Energy Consumption Monitoring: Digital twins can track energy usage across the entire production process, from heating and cooling to mixing and separation. By visualising energy data, a digital twin can help you identify inefficiencies and suggest process adjustments to reduce energy consumption without compromising productivity.
Digital Twins in Mining
Mining operations involve complex, large-scale processes, often in remote and harsh environments. A digital twin—a real-time virtual replica of physical assets, processes, or systems—helps mining companies improve operational efficiency, enhance safety, and reduce costs. By integrating real-time data from equipment, geological models, and environmental factors, digital twins can support predictive insights, visualise simulated scenarios, and enable more informed decision-making.
Mine Planning and Design Optimization
Simulate the entire mine lifecycle, allowing engineers to test different design strategies and optimize layouts based on factors like cost, extraction efficiency, and safety.
Equipment Maintenance and Reliability
By using a digital twin to monitor the condition of equipment (e.g., trucks, drills, conveyors) in real time, mining companies can apply predictive maintenance. This allows maintenance teams to forecast when equipment will fail and perform repairs before breakdowns occur.
Operational Efficiency and Resource Optimization
Enable real-time tracking of operations, including resource flow, material movement, and energy consumption. A digital twin can help optimize production schedules, minimize energy use, and increase throughput by continuously adjusting based on real-time data.
Safety and Risk
Management
Simulate various risk scenarios, such as equipment malfunctions, geological events, or emergency situations. By analyzing real-time data, it can predict and prevent accidents, improve emergency response plans, and optimize safety protocols.
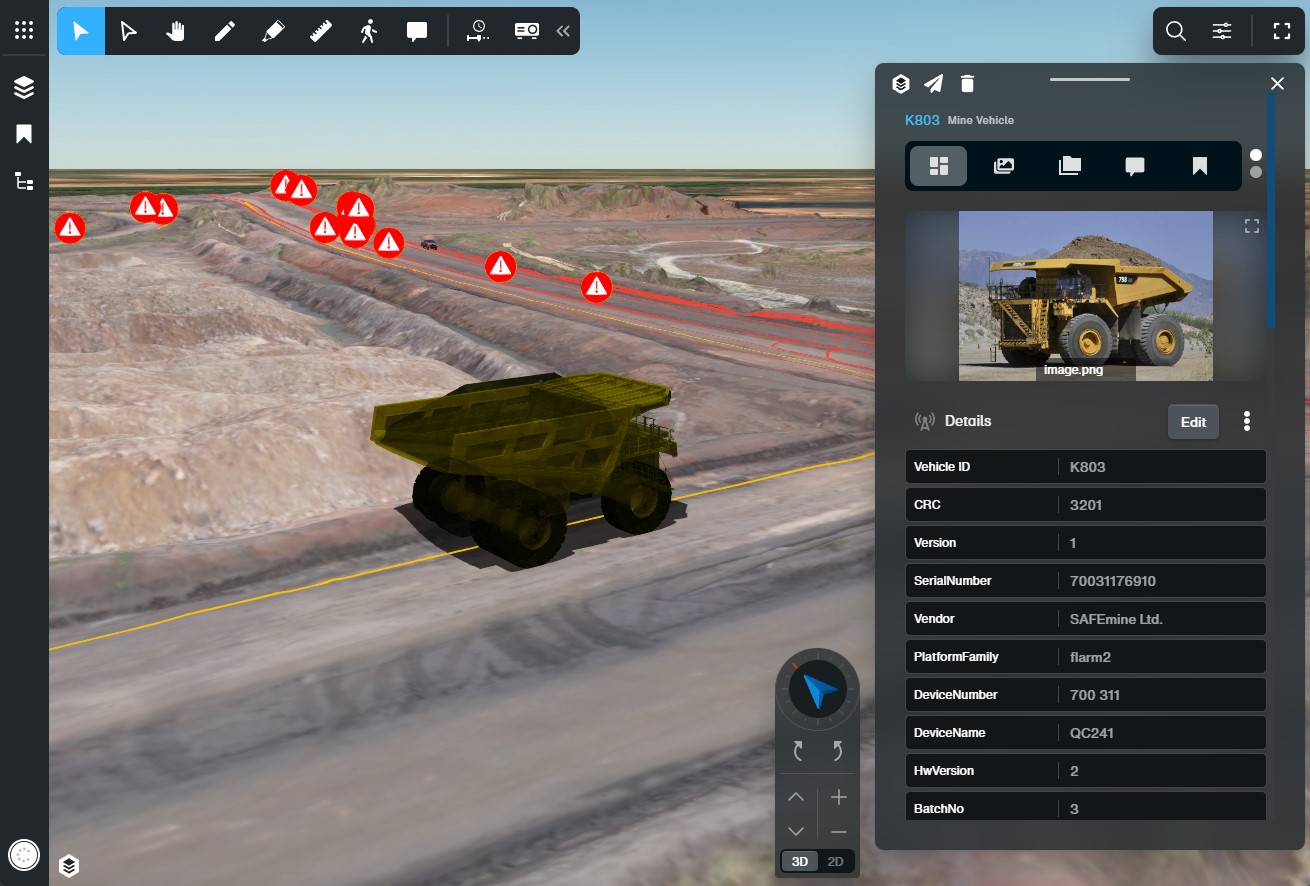
Maximise operational efficiency
Optimize operations by creating a virtual replica of the entire mining process
Tracking Operational Performance: Provide a real-time view of equipment performance, including productivity rates, equipment health, and load capacities. Tracks how much material is moved by trucks or the efficiency of crushers in processing ore.
Optimizing Resource Usage: Use real-time data to optimize energy consumption by scheduling high-energy tasks during off-peak times or improving the efficiency of equipment. Track water and fuel usage to ensure resources are not being wasted.
Remote Decision Making: Use the digital twin to monitor and control mining activities remotely, making adjustments based on real-time data without the need to be physically present at the mine site.
Industry Use Cases
Companies that love what we’re doing
Companies that love what we’re doing